Pharmacy inventory management: Maintaining availability despite complexity
Mar 15, 2022 • 6 min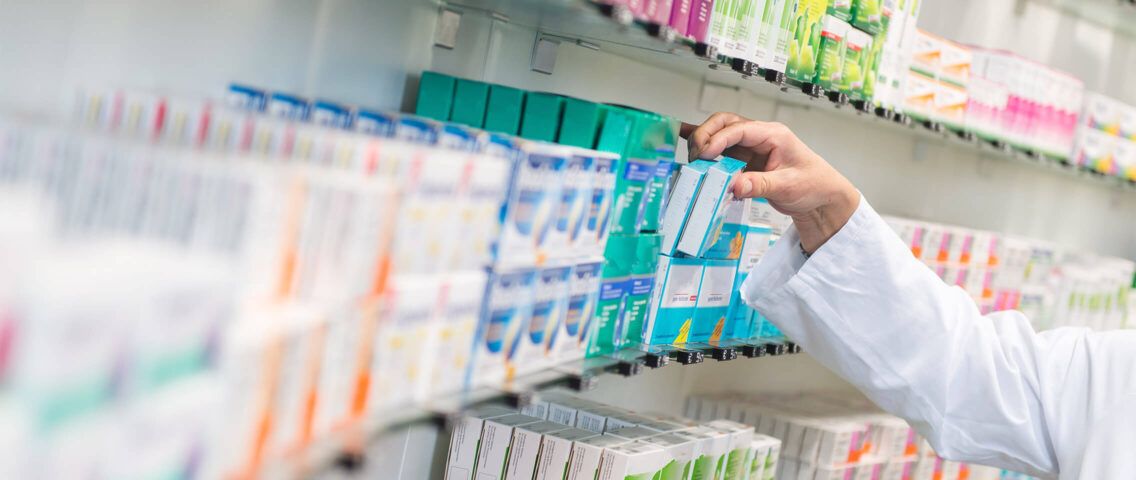
No retailer has it easy when it comes to managing inventory. Pharmacies, though, could make a defensible argument for having to sort through the most complex inventory considerations.
On any given day, a pharmacy’s inventory planning team must:
- Manage highly regulated prescription medications that vary by country and region, while also…
- Balancing fast and slow-moving inventory with different shelf lives and storage requirements, while also…
- Accounting for limited promotional levers, since prescriptions are never impulse buys, while also…
- Adapting to shifting regulations and insurance policies that make demand hard to predict, while also…
- Overseeing thousands of SKUs with vastly different prescription rates.
Add the adoption of omnichannel models, and the complexity of the pharmaceutical system only compounds.
These cascading complications mean that no pharmacy can hope to efficiently maintain customer satisfaction and protect margins without the help of a sophisticated, AI-powered inventory management solution. The right software will help teams couple automation with human expertise to address the unique compliance and substitution challenges of pharmaceutical retail.
Why precise inventory management drives pharmacy competitiveness
Customers expect their pharmacy to have the medications they need when they need them. This expectation makes a pharmacy’s most critical inventory challenge determining which medications to stock at all times versus which ones to order from suppliers as needed.
This balancing act requires pharmacies to maintain precise inventory levels while responding to fluctuating demand. Relying too heavily on one-off orders for out-of-stock medications leads directly to lost sales and customer dissatisfaction. But overstocking ties up capital and risks spoilage, damaging already tight margins.
Pharmacies face particularly severe consequences for stockouts. Customers won’t accept substitute medications without consultation with their healthcare provider. A single out-of-stock medication can send a customer directly to a competitor, costing the business individual sale and, potentially, all future business.
Understanding medication inventory categories
Managing pharmacy inventory effectively requires recognizing that different medications have vastly different demand patterns and inventory requirements. Fast-moving and slow-moving inventory in particular require distinct approaches.
Fast movers: High volume, predictable demand
Fast-moving medications — like those for blood pressure management — typically don’t require significant financial investment. Pharmacies can maintain high availability for these high-demand items without risking their bottom line. The question becomes how much to keep on hand and how frequently to replenish.
For these medications, automated replenishment systems based on historical sales data can effectively maintain appropriate stock levels. The challenge isn’t whether to stock these items, but how to optimize ordering frequency and quantities to balance storage constraints with consistent availability.
Slow movers: Low volume, unpredictable demand
Managing slower-moving prescriptions presents an entirely different challenge. With limited sales data available, AI-powered demand forecasting becomes difficult.
For these medications, pharmacies need data-driven approaches to determine:
- Whether a slow mover should be stocked at a particular location
- When to stock or restock these medications
- What quantity to maintain in inventory
The key decision is whether to keep these medications in regular inventory or order them only when specifically requested. This decision requires balancing the cost of maintaining inventory against the risk of lost sales from unavailability.
Successfully managing both medication types requires a flexible inventory planning system. Supply chain planners must configure solutions that automate replenishment for fast movers while allowing pharmacists to input local demand information for slow-moving medications.
Establishing central rules with local flexibility
Every pharmacy strives to optimize prescription inventory, but optimal inventory differs across locations. Busy locations with high turnover and minimal storage face different challenges than locations with less footfall but ample storage or those fulfilling both in-person and online orders.
Advanced inventory management systems can automate many replenishment tasks when given sufficient input data on sales frequency and product costs. These systems must manage different medication categories while accounting for:
- Local demand variations
- Changing government subsidies and insurance rules
- New medications entering the market
The system must also offer enough flexibility for users to customize replenishment strategies for specific locations. While fast-moving medications can follow standard retail replenishment patterns, slow movers require specialized approaches to prevent lost sales from repeated unavailability.
An effective system combines lost sales tracking with special order data (instances where customers waited for medication delivery) to determine whether to permanently stock a slow-mover or continue as-needed replenishment.
Planners might configure the system to automatically add a medication to a location’s permanent assortment after four requests — for example, two lost sales and two special orders. This combination would trigger the rule, automatically adding the product to future assortments.
But automating assortment decisions is just the beginning. The system must continuously recalculate forecasts and safety stocks to support automated replenishment throughout varying product lifecycles.
Navigating substitutions in pharmacy inventory
Medications go out of stock despite best planning efforts. Pharmacies face constraints that don’t apply to other retailers in these situations. A pharmacist can’t simply substitute one medication for another. The pharmacist must consult with the prescribing healthcare provider to determine acceptable substitutions.
The only permissible substitution might be package size variations, like replacing one 100-capsule pack with two 50-tablet packs of identical medication. Whereas grocery store customers can easily choose another cereal brand, pharmacies operate under strict substitution constraints.
Substitutions are occasionally necessary but best avoided. When pharmacies do need to replace out-of-stock medications with available alternatives, they need an inventory management system that accounts for these substitutions and automatically adjusts future replenishment orders.
Any effective pharmacy inventory system must track substitution patterns and incorporate this data into AI-powered forecasting and replenishment decisions. This ensures that when substitutions do occur, the system learns from these instances and adjusts ordering patterns accordingly.
Managing “preferred” generic medications
Multiple manufacturers produce the same generic medication, requiring pharmacies to order from the most appropriate supplier based on current circumstances. Customers may not notice the switch from one manufacturer’s generic to another, but these substitutions create inventory management challenges similar to other medication substitutions.
In many markets, government agencies or insurance companies designate specific manufacturers and their generic products as “preferred.” This preferred status means:
- The medication will be subsidized or discounted for pharmacies and customers
- Other manufacturers’ versions won’t receive the same benefits
- Pharmacies have financial incentives to stock preferred versions
These designations change periodically based on local regulations. Swedish government entities publish monthly updates on preferred generics, while Danish authorities update designations every two weeks.
Preferred status scenarios include:
- Multiple manufacturers holding preferred status simultaneously
- No manufacturers receiving designation
- Regional variations in preferences
Medication demand typically remains stable regardless of manufacturer changes. Customers expect prompt fulfillment from available inventory, regardless of which company manufactured the generic medication.
Pharmacies need inventory systems that can:
- Automatically identify preferred manufacturer designations
- Apply established rules for supplier selection
- Transfer demand data to newly preferred products
- Maintain availability during status changes
These capabilities ensure pharmacies can seamlessly navigate preferred status changes without disrupting medication availability or customer experience. With the right system in place, what could be a complex supply management challenge becomes a routine, automated process.
Balancing automation with pharmacist expertise
Managing both standard inventory and complex scenarios like generic substitutions requires finding the right balance between technological automation and human judgment. While automated systems excel at processing large volumes of data and applying consistent rules, pharmacist expertise remains essential for nuanced decisions that require local market knowledge and clinical understanding.
Successful prescription inventory management requires a planning tool that automates AI-powered, chain-wide forecasting and replenishment while allowing pharmacists to share local trends and make location-specific modifications.
Automating common medication management enables local teams to focus their expertise on exceptions and manual order modifications based on local demand patterns. This balance ensures customers at any location can access the medications they need when they need them.
The appropriate balance between automation and human judgment varies based on medication category:
- Fast-moving medications can rely heavily on automated systems with minimal human intervention
- Slow-moving medications benefit from pharmacist input on local demand patterns and patient needs
- Substitution scenarios often require pharmacist expertise to determine appropriate alternatives
- Generic medication selection can be guided by automated rules but may need pharmacist oversight
The goal is to leverage automation for predictable, data-driven decisions while preserving pharmacist time for scenarios requiring clinical judgment and local market knowledge.
A comprehensive inventory system for pharmacy success
The inherent complexity of managing their inventory means pharmacies need systems that address all these requirements in a unified, coherent way. A truly comprehensive inventory management solution must incorporate capabilities for each aspect of pharmacy operations while maintaining user-friendly interfaces that support both automated and manual processes.
To successfully navigate all these complexities, pharmacies need inventory planning and management systems that can:
- Identify medication demand within groups with the same active ingredient
- Account for various types of substitutions
- Automate replenishment across manufacturers when preferred status changes
- Balance chain-wide rules with location-specific needs
- Support both automated and manual decision-making processes
Sophisticated automation handles these complexities, allowing pharmacy planners to redirect their expertise to higher-value activities that maximize their skills and experience.
Drive competitive advantage through effective inventory management
Pharmacy inventory management presents unique challenges, but pharmacies share fundamental goals with other retailers: satisfying customers and protecting margins. Intelligent technology that balances product availability with storage constraints helps pharmacies serve customers and maintain competitiveness in an ever-changing market.
Effective pharmacy inventory management combines fundamental practices like balancing fast and slow-moving medications with specialized capabilities for handling substitutions and generic medication changes. With the right inventory management system, pharmacies can navigate these complexities while maintaining exceptional customer service and operational efficiency — ultimately driving both patient satisfaction and business performance.