Fresh optimization: Catching grocery retail’s white whale
Jan 19, 2024 • 5 min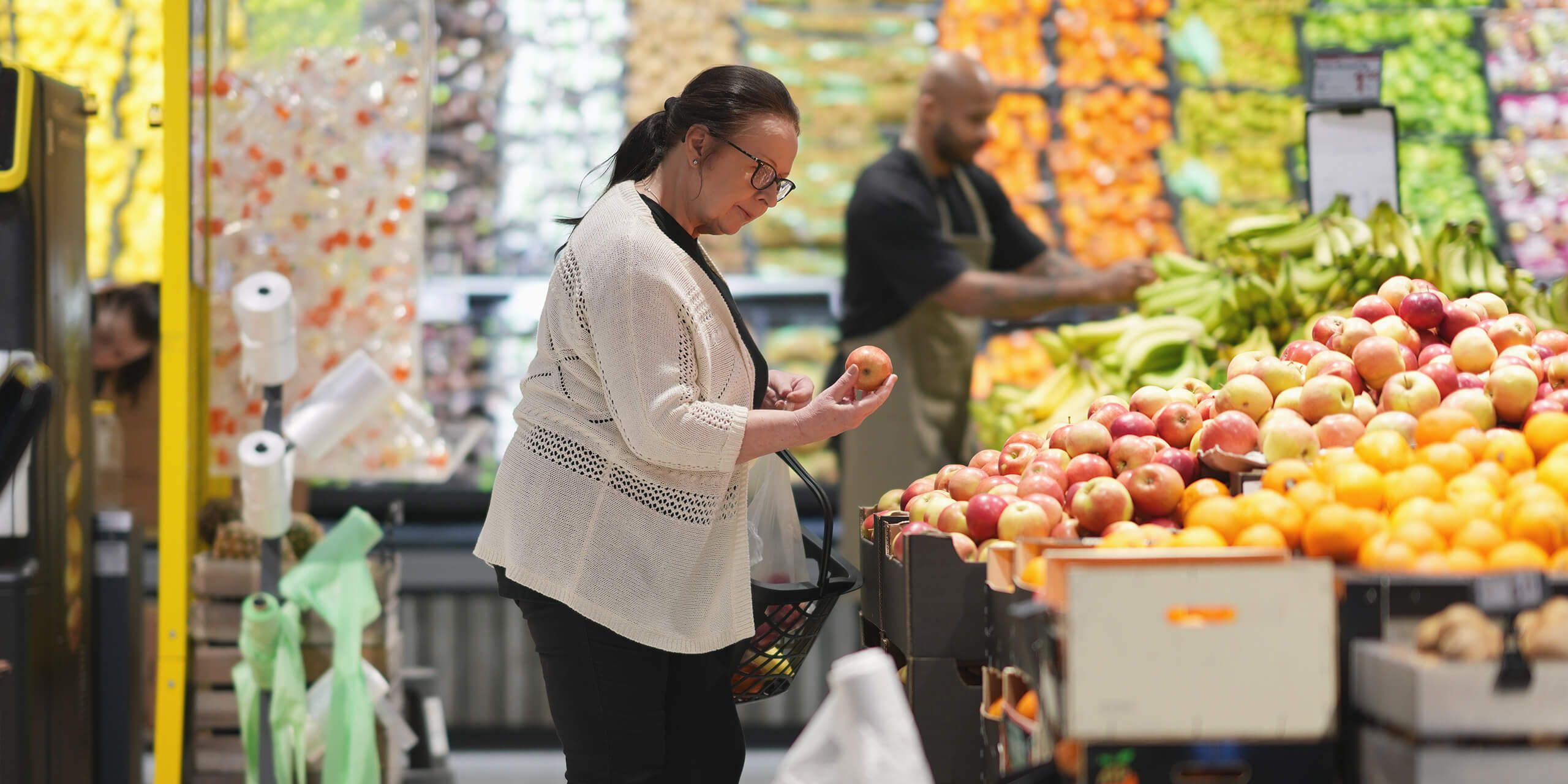
For many retailers, fresh management remains the final fish to catch when introducing new or upgraded technologies to improve demand forecasting and optimize replenishment. The unique characteristics of managing fresh grocery retail have made it a hidden treasure amid a sea of AI and machine learning technologies. Still, many businesses rely on base-level solutions and fear taking the next investment leap. That situation must – and now can – change. It is time to be bold and wave goodbye to imperfect inventory data in fresh grocery.
Considering the importance of managing fresh inventory, why has it been such a challenging beast to tackle so far? As a fast-moving product assortment, fresh’s primary challenge comes from the need to juggle both short- and long-term inventory management. From a stock perspective, grocers must make real-time decisions for the next day or week. Simultaneously, they must translate evident trends into future decisions that impact business strategies.
Grocery retailers are under pressure to anticipate required stock levels while reconciling the products’ various and, in many cases, rapid spoilage rates. However, the biggest issue is poor or completely lacking inventory data. When so many companies strive for improved carbon footprints, the sweet spot of avoiding empty shelves and customer frustration while ensuring availability and presentation without driving waste is a narrow plank to walk.
On top of all the inherent challenges of managing fresh inventory, retailers must cope with labor shortages and high staff turnovers that leave them struggling to leverage long-term skills and experience.
There has long been an acknowledgement that technology is critical to finding the availability-waste sweet spot, mitigating labor issues and addressing the sheer pace of fresh retail. However, until now, there haven’t been enough viable solutions to convert that acknowledgement into action.
Spoilage and shrink: An imperfect combination
RELEX has sought to address a cliché that has almost become a running joke in fresh grocery in recent years: “Inventory data is never correct”. It’s an exaggeration, perhaps, but it reflects the unique challenge of products like fruits and vegetables.
They are more challenging than any other products to monitor across the supply chain journey, up to – and including – the point of sale. Produce is frequently sold loose, creating an immediate difficulty in terms of monitoring. Each item spoils, but at a different rate to every other item – even those in the same batch. Occasionally, items spoil during distribution, making “How many actually arrived at the store?” a common question.
There is also the issue of shrink. Products may lose moisture, which can skew weight-based modes of monitoring or tracking inventory. Stores may label items incorrectly or accidentally mix similar products or batches. Theft, loss, and unrecorded waste also lead to shrink and compromised inventory data.
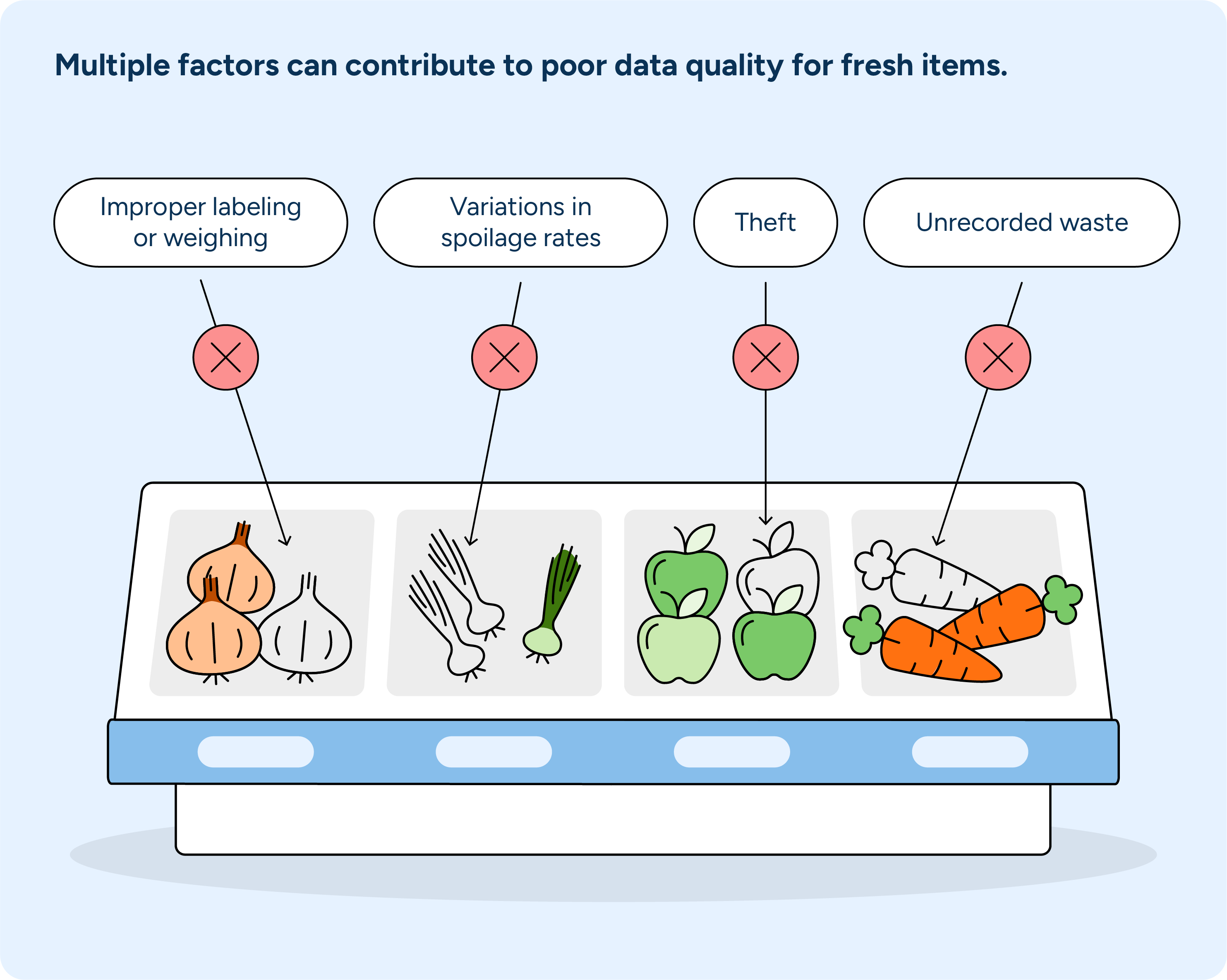
These issues result in imperfect or missing inventory data, which is a constant challenge for retailers and a significant barrier to introducing technology to streamline the ordering process. Typically, at that stage, best-guess estimates of the ordering needs are conducted by store associates in the fresh produce departments, while in other parts of the store, the ordering could be more automated.
No more firefighting: It’s time to rethink the process
The good news is that the challenges retailers have encountered when managing fresh grocery inventory can now be overcome.
One option is maintaining manual processes and allocating enough time and people for inventory counting and ordering. This calls for a level of expertise which is often scarce to get and retain.
Another way is to use technology designed for ease of use by store associates and streamline the key processes with smart recommendations provided through an easy-to-use mobile app, ultimately leading to fewer manual touchpoints. When the process and tool are based on data and fit-for-purpose, it will be easy for people with different expertise levels to adopt and achieve great outcomes.
AI is a critical element in automation, which should augment associates’ capabilities and expertise. While AI certainly isn’t a replacement for their decision-making skills, it can guide and drive speed, efficiency, and accuracy to their daily tasks, enabling them to spend less time on manual number-crunching and more time on customer service.
Getting as far away from imperfect as possible with predictive inventory
Variations in spoilage rates, in-store conditions, sizes, and even seasons are a few of the complexities that have made fresh categories historically tricky for retailers to manage. These complexities naturally result in imperfect inventory data sets, as the transition from supplier to store to consumer leads to information gaps.
Fresh optimization from RELEX simplifies the intricacies of store inventory management and ordering. This innovative solution offers a clear perspective on short- and long-term customer demand, on-hand inventory and spoilage projections, significantly reducing the need for manual line-by-line inventory counts and order placements by store associates.
When initial balance data is of poor quality or nonexistent, as is often the case with fresh produce, RELEX can, from the transactional data, construct an accurate view of on-hand inventory. Leveraging artificial intelligence, the system further identifies data anomalies and either notifies the store through an easy-to-use mobile app, suggests cycle counts based on inventory accuracy development, or automates corrections in inventory drift. This is what we call predictive inventory.
Store associates can then prioritize their attention on flagged exceptions, leaving the system to handle orders without issues if they choose to do so. While store personnel are empowered with new technology and apps, they will have good visibility of the critical data and can make amendments as appropriate. Furthermore, those amendments are used to improve inventory predictions. So, it is a closed-loop process where calculations get better through new data and insights.
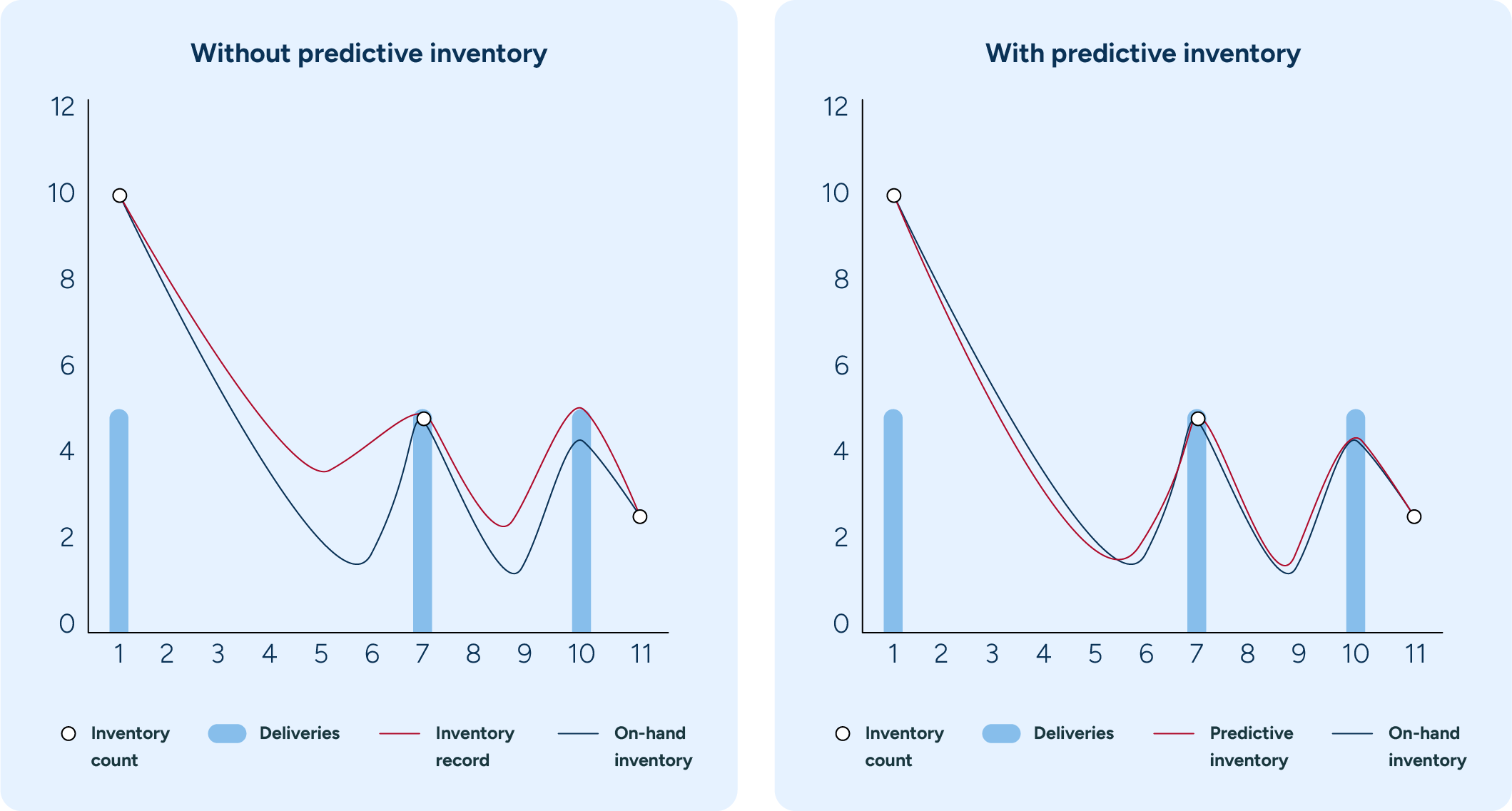
While inventory inaccuracies are especially challenging in fresh produce, they pose significant issues in other departments. The noteworthy aspect is that the predictive inventory solution can effectively identify phantom inventory across various departments. This is a crucial breakthrough, as phantom inventory is a well-known problem causing customer frustration and lost sales over extended periods.
All that is needed is one solution. A solution that runs in the cloud but can be integrated into retailers’ other software. Configurable and flexible enough to be customized to a retailer’s unique strategies, objectives, and priorities, it is a solution that can yield unrivalled accuracy for a product group that has been historically problematic.
Even if “perfect data” isn’t possible, recent advances in AI and machine learning have made great strides for retailers and enabled them to use data that would have previously been deemed useless. Fresh retailers finally have the chance to get as far away from ‘imperfect’ as possible—an opportunity to catch their white whale.
Learn more about how RELEX can help you get a handle on fresh optimization.