Fresh and center-store inventory management: The need for a dual approach
Nov 22, 2024 • 6 min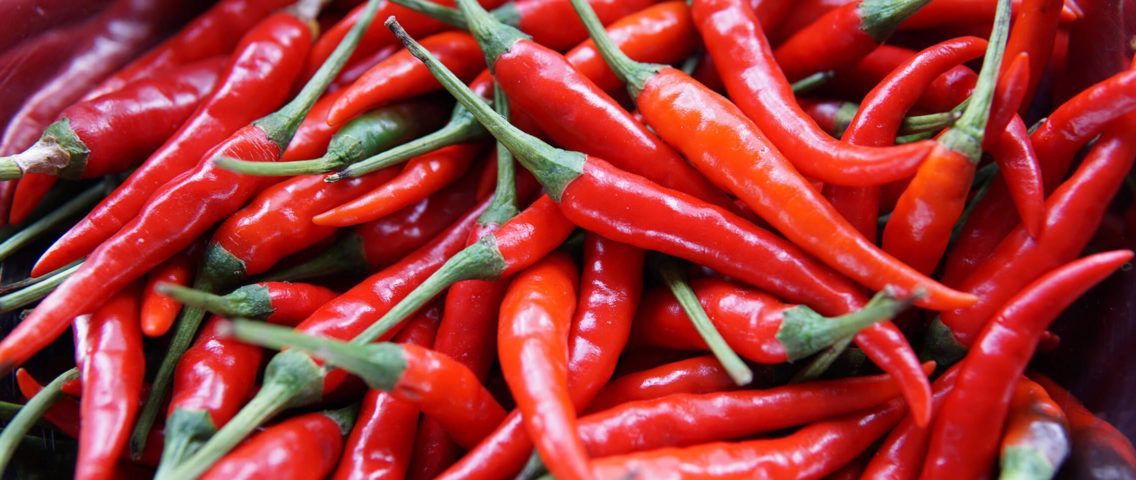
Supermarkets and discounters are masters of efficiency in their respective niches — but not so efficient outside of them.
Supermarkets have mastered the agility and responsiveness required for fresh food but often lack efficiency with their center-store inventory management. For discounters, the problem is inverted. They’ve streamlined center-store inventory management but lack the speed and adaptability to manage fresh food efficiently.
Supermarkets and discounters seek to branch out from their niches to appeal to a broader, more price-sensitive consumer base. However, what works for center-store inventory management does not work for fresh food management, leaving retailers to puzzle over how to mitigate their weak spots without sacrificing existing efficiency.
Food retailers must adapt their processes to become efficient in both fresh food and center-store inventory management to stay competitive in the current market — and they’ll need a robust forecasting and replenishment platform to do it.
The keys to managing fresh products
Supermarkets know too well how difficult it is to manage fresh inventory. They must deliver products at the peak of freshness to appeal to consumers who base much of their purchasing decisions on appearance. But fresh food expires quickly, and spoilage concerns limit retailers’ ability to maintain predetermined safety stock levels for fresh products.
This inability to carry static amounts of safety stock also hurts fresh food retailers. Demand for food products is highly volatile and can change based on factors ranging from inflation to hot social media trends. Reduced safety stock levels help prevent spoilage, but low levels can also result in stockouts that hurt companies when demand surges.
A single ill-timed stockout could influence otherwise loyal customers to avoid shopping at a retailer altogether.
The negative impact of stockouts extends beyond the direct cost of missing out on a single-item purchase. Customers disappointed by stockouts of high-priority fresh items may abandon their cart to seek out a retailer that carries what they need. A single ill-timed stockout could even influence otherwise loyal customers to avoid shopping at a retailer altogether.
Balancing spoilage concerns and stockout worries is essential to successful fresh food inventory management. An effective fresh management strategy requires three facets: dynamic safety stock optimization, just-in-time delivery, and granular demand forecasting.
Dynamic safety stocks
A company implementing dynamic safety stock optimization sets unique levels for each product per day, helping retailers stay prepared for high-demand periods like weekends, the first of each month, and holidays. As the name suggests, the actual number of products fluctuates depending on consumer demand forecasts. When demand surges, the safety stock level increases; when demand wanes, the safety stock level decreases.
Proper utilization of dynamic safety stocks requires AI-powered planning software that can identify sudden consumer demand shifts and adjust stock levels accordingly to avoid overstocking or understocking fresh products. When done right, this helps retailers maintain the appropriate number of goods on hand to satisfy their customers’ needs without risking expensive food waste.
Just-in-time delivery
The ability to set dynamic safety stocks is only possible with just-in-time deliveries, which enable retailers to place orders based on immediate demand needs and receive the ordered products quickly. Just-in-time deliveries let retailers hold only the minimum amount of product needed based on demand forecasts to help:
- Ensure optimal freshness.
- Minimize spoilage.
- Reduce carrying costs.
Just-in-time deliveries keep products fresh and reduce waste, but they do require an element of workforce planning. It’s essential for retailers that adhere to just-in-time delivery to account for the frequency of the deliveries themselves as well as the repeated replenishment of fresh products on the store floor. Strategic staff scheduling aligned with delivery volume — increasing coverage during peak periods and reducing staffing during slower intervals — optimizes labor costs while maintaining operational efficiency.
READ MORE: Unlock profitability with replenishment optimization
Granular demand forecasting
Both dynamic safety stocks and just-in-time delivery require a more zoomed-in understanding of demand than manual processes or obsolete software can handle. Planning platforms use machine learning to create granular demand forecasts that consider a range of factors, such as:
- Weekday-related variation, like a surge of produce purchases ahead of the weekend.
- Local events, like conferences or nearby construction projects, that impact foot traffic to the store.
- Weather forecasts.
- Competitor promotions and pricing.
These granular forecasts allow retailers to retain the planning agility needed to succeed in fresh inventory management.
The keys to managing center-store products
Center-store inventory management necessitates a different approach to that of fresh products. Whereas fresh products require responsiveness and adaptability, center-store inventory management success hinges on operational efficiency.
The difference boils down to a simple fact: center-store products don’t have the same time sensitivity as fresh products because they don’t have as high a risk of waste or spoilage. Retailers managing center-store goods must maximize capacity utilization and minimize handling costs throughout their supply chains, including in their stores.
Retailers can accomplish this through space-aware replenishment, store planogram optimization, and dynamic batch size optimization.
Space-aware replenishment
Companies managing center-store items should aim for each delivery to fill store shelves completely rather than just the amount needed to meet demand until the next delivery — a concept called space-aware replenishment.
Compare this with the just-in-time delivery approach used with fresh products. A retailer applying this approach to center-store products will quickly drive up operational costs. Instead, retailers must minimize the number of touches required to get center-store products to the store shelf.
Store planogram optimization
Retailers can optimize store planograms to match daily demand and replenishment schedules, ensuring more goods fit straight on the shelf. Direct-to-shelf replenishment reduces the need for staff to move products between backroom storage and the sales floor.
Dynamic batch size optimization
Retailers can further reduce costs with dynamically optimized batch sizes based on seasonal demand and available space in each store. (Think ordering case packs rather than pallets.) Retailers can also reduce costs in both distribution centers and stores when goods are delivered in reasonably large quantities directly to the store shelf.
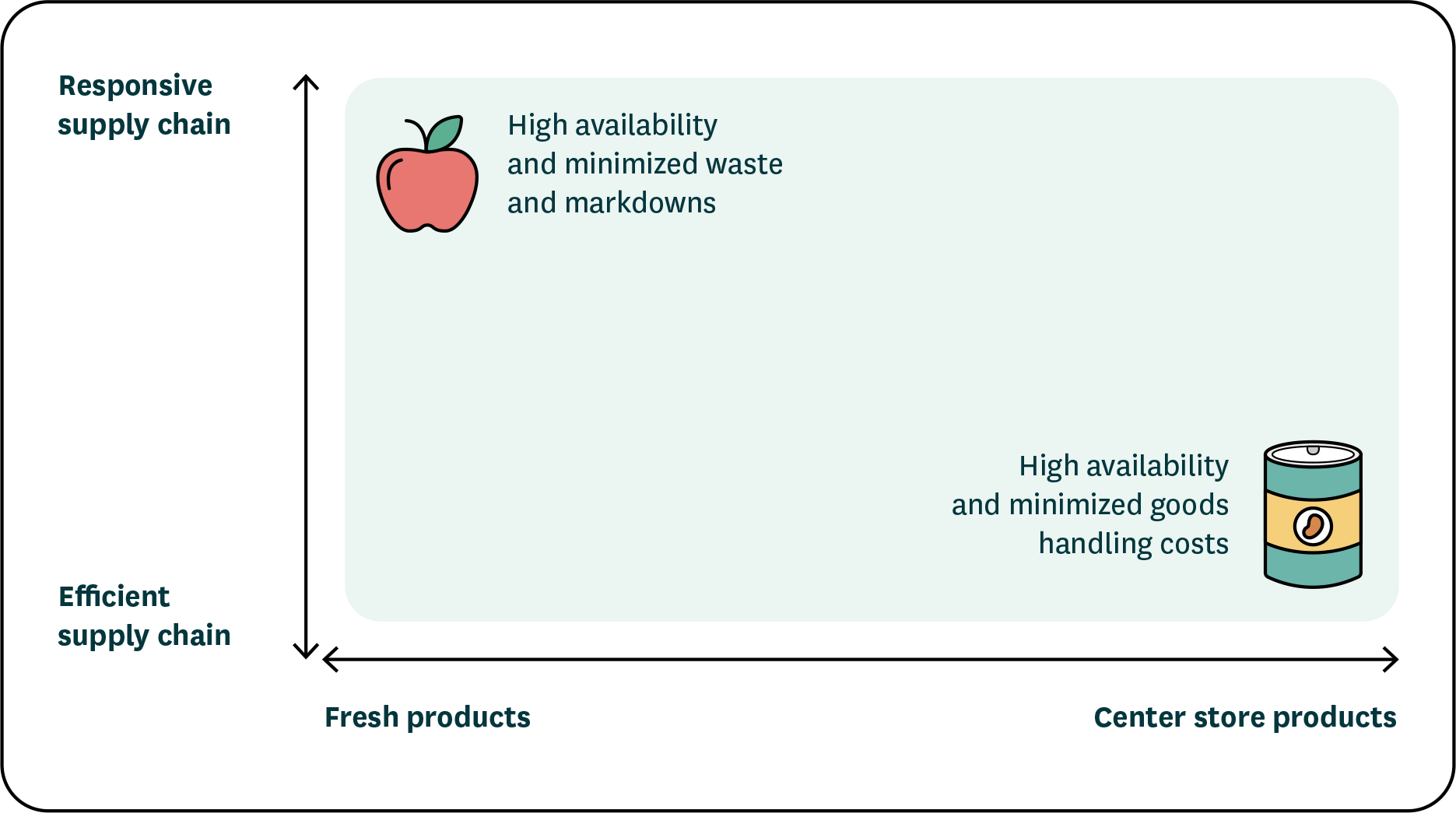
What is the key to fresh and center-store inventory management alignment? A capable software solution
The management of fresh and center-store products couldn’t be more different. So, how do retailers excel at both approaches?
Modern forecasting and replenishment software allows retailers to execute agile supply chain management (of fresh products) and lean supply chain management (of center-store products) in parallel. The best systems go even further, jointly optimizing both product flows for the highest productivity through proactive capacity management.
The application of main replenishment days exemplifies this alignment. Main replenishment days concentrate the replenishment of related and similarly located center-store products (like detergents and other laundry products) to specific weekdays. This improves replenishment efficiency, reducing staff movement throughout the store.
Main replenishment days for fresh products create a smoother overall goods flow throughout the supply chain.
However, food retailers can also optimize main replenishment days around the delivery needs of the fresh assortment. Deliveries of these goods often peak later in the week in preparation for consumers’ weekend shopping. Main replenishment days for fresh products create a smoother overall goods flow throughout the supply chain, enabling better capacity utilization and easier work-shift planning.
French convenience store retailer Franprix is a terrific real-world example of delivery flow smoothing in action. Franprix uses RELEX’s AI-based flow smoothing optimization to level their goods flow throughout the week, leading to:
- A more evenly distributed workload in stores.
- Less congested stores on peak sales days.
- A 20% reduction in distribution center workload on their highest-volume weekday.
The best of both worlds
It’s tough to specialize in the efficient management of either fresh or center-store products, making the challenges of managing both seem monumental. However, retailers who take advantage of the latest forecasting and replenishment technology can achieve the responsiveness required by a high-quality fresh offering while simultaneously planning the replenishment of their center-store products for cost-efficiency.
The result? Reduced spoilage, improved availability, reduced operational costs, smoother and more predictable product flows, and — most importantly — happier customers.